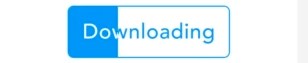
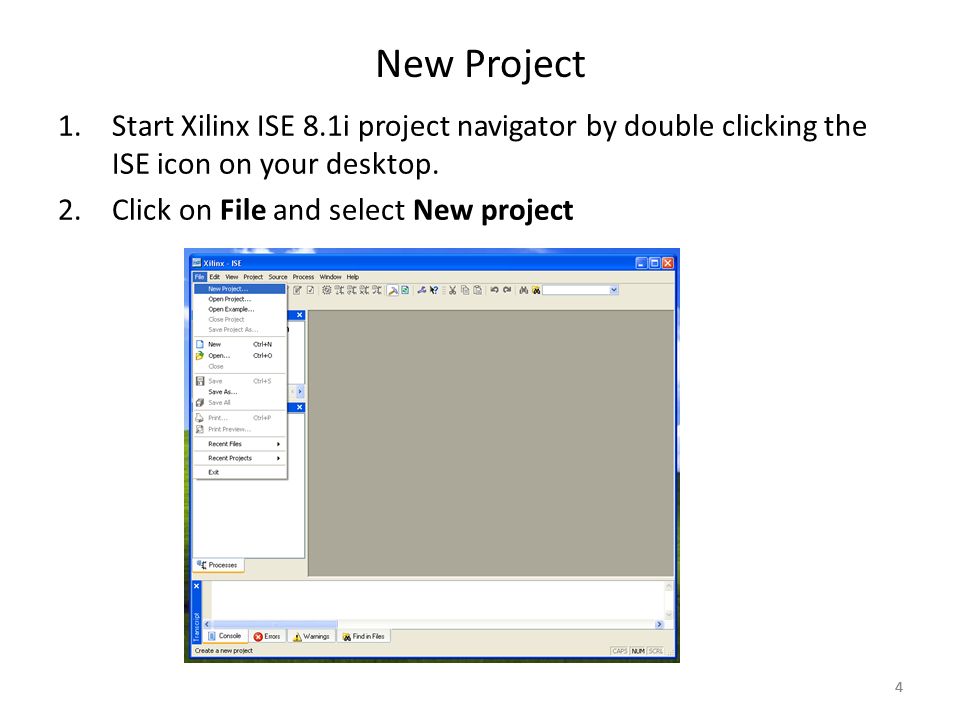
This is especially significant for modern in-vehicle frameworks, where reliability is of principle significance.Īn infrared sensor circuit is one of the basic and popular sensor modules in an electronic device. Besides, FPGA’s empower frameworks to be worked with ensured deterministic outcomes. This additionally results in reduction in cost as well as power consumption. Along with the execution support, such frameworks give a platform for realizing various circuit on same equipment with complete segregation, utilizing hard partitioning, and partial or complete reconfiguration. The re-configurability of the FPGA permits designers to manufacture customized circuits having high efficiency and low power consumption, along with having the benefit of flexibility of software system. Reconfigurable processing elements like Field Programmable Gate Arrays (FPGAs) can be used as the possible alternative. If independent CAN controller is utilized, there is a cost overhead as an additional IC is required, expanding the expense of the framework. This is a serious factor in modern systems, where latency is an issue. Microcontrollers with incorporated CAN interface endure an execution penalty, as the microcontroller is responsible for message transmission and receiving, other than examining inputs and driving outputs. The rs232 has 9-pins that mean female to USB is used and transmission is done.

In this SPARATAN 3e kit is used for the implementation purpose.Here rs232 cable also used for the purpose of storing and transmitting information to the pc. The parallel ports are connected to the pc and the JTAG is connected to the FPGA kit.The JTAG is used for the purpose of program load. Theinformationis stored in SAR and bit by bit shifting process takes finally the outputs are come into the Dout.The JTAG is used here. Thecomparator compares the input signal with that the reference signals. Here the selection of input is the first pin channel as 000.The sigma-delta conversion is done by using the advanced IC MCP3208.Here the input is connected in real time.The IC contains 8-channels.Each and every channel consists of 12-bit resolution.The input channel acts as mux.Based on control logic it can give the output.After the output is sampled and hold value and give to the comparator block. The second pin is connected to the channel of IC pin. The figure shows the main block diagram of Sigma-Delta ADC.In this input is potentiometer and It consists of 3-terminals supply varying output display and gnd.The supply pin is connected to the IC supply pin similarly gnd. It is suitable for hardware implementation.
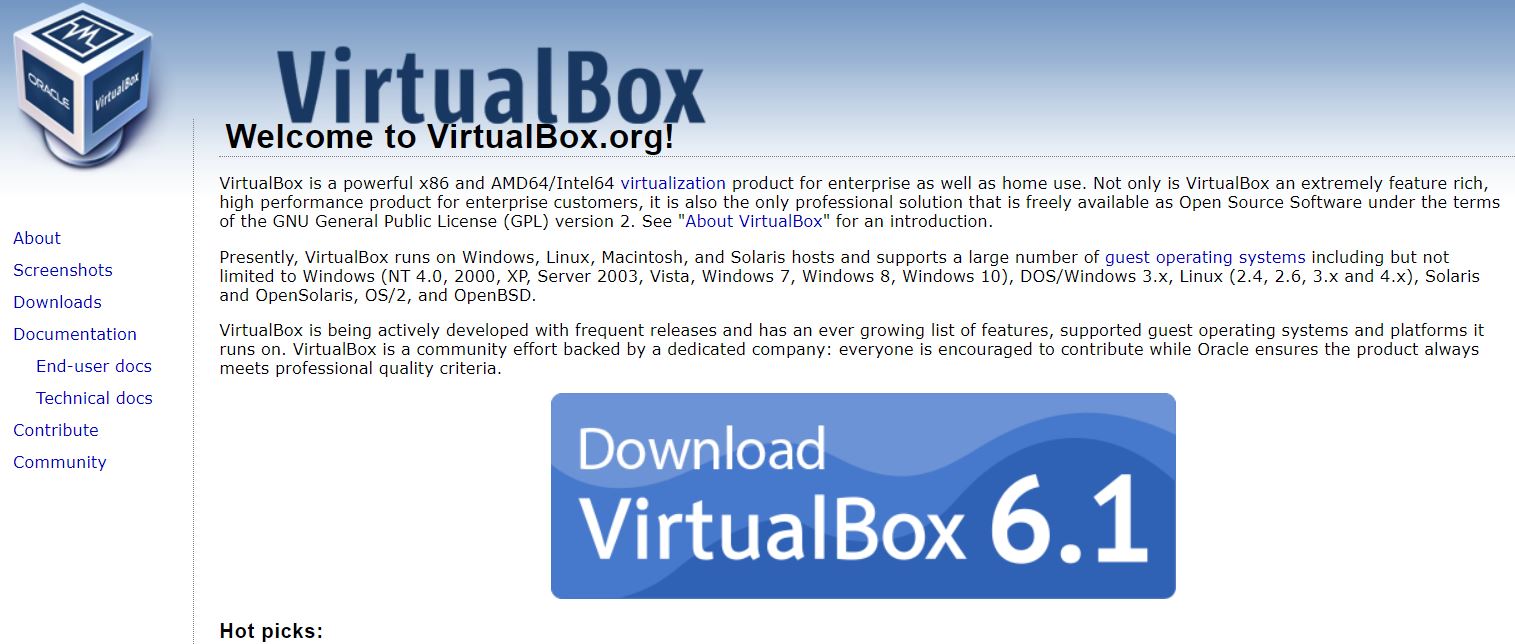
To overcome these problems the Sigma-Delta ADC is designed in Xilinx ISE 14.6 and it is implemented using SPARTAN 3e kit.
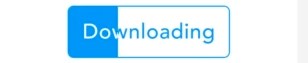